8 лучших грунтов-антикоров — описание, особенности, область применения
Грунт необходим любому металлу под покраску, будь то автомобиль, металлический забор или кованое изделие. Гораздо выгоднее владельцу, если грунт – антикоррозийный. Ведь именно тогда о коррозии можно забыть, а изделие будет служить и радовать своим видом долгие годы. Еще удобнее, если грунт в аэрозольном баллоне, что дает массу дополнительных преимуществ:
- Состав готов к нанесению – нужно только потрясти.
- Не нужны кисти, валики и прочее – все, что нужно уже у вас в руках.
- Можно тщательно покрыть мелкие детали и труднодоступные места.
- С нанесением легко справится не профессионал.
- Стоимость спреев — грунтов – ниже, чем у других антикоррозийных покрытий.
- Средство в баллончике расходуется экономнее.
Чтобы облегчить вам выбор, мы представляем
Топ 8 лучших антикоррозийных грунтов в аэрозольных упаковках
1.
Преимущества:
- Наносится в считанные минуты.
- Содержит 95% цинка.
- Обладает высокой степенью защиты от коррозии.
- Защищает от воздействий окружающей среды.
- Сочетается с большинством современных ЛКМ.
- Не препятствует сварке и не портит сварной шов.
- Сохраняет плотности однородность покрытия долгие годы.
Активно применяется в промышленности, строительстве, в энергетике и области нефтегазовых работ, в автомобилестроении, обработке и покраске автомобилей, их защите от коррозии, в строительстве гидросооружения и дорог.
2. Loctite 7800 — защитное антикоррозионное покрытие для черных металлов. Работает как грунт, финишное покрытие, или промежуточный слой в многослойных системах защиты.
Преимущества:
- Содержит высокое содержание цинка и синтетические смолы.
- Почти не имеет запаха.
- Защищает от электрохимической коррозии, в том числе сварные швы.
- Дает металлам эффективную защиту от коррозии и приятный внешний вид.
Часто применяется для защиты сварных швов, узлов и соединений металлических конструкций. Используется для ремонта и восстановления оцинкованных деталей: барьеров на автостраде, труб, фланцев, резервуаров, монтаже трубопроводов, кровельных и кузнечных работах.
3. WEICON Rust Protection 2000 PLUS – антикоррозийное покрытие высокой мощности, используется для долговременной катодной защиты всех металлических поверхностей.
Преимущества:
- В составе мельчайшие хлопья цинка, связующее вещество и ясные металл-оксид пигменты.
- Создает надежный, быстросохнущий и прочный слой.
- Устойчив к самым высоким температурам до + 500 градусов.
- Выдержал испытания соленым туманом в течение 550 часов – ни следа коррозии.
- Выпускается в двух цветах: темно и светло-сером.
Применяется как эффективный антикоррозийный грунт и для восстановления поврежденных цинковых покрытий, отлично подходит для точечной сварки.
4. Tectyl Zinc ML– считается самым эффективным и популярным защитным спреем-грунтом против коррозии.
Преимущества:
- Обладает водоотталкивающим эффектом.
- Сочетает в себе все преимущества средств последних поколений.
- Содержит воск, растворители, диспергированный цинк и ингибиторы коррозии.
- Обладает свойствами защиты от всех видов почв, отобранных в различных городках России.
Применяется для антикоррозионной обработки стыков, швов, внутренних полостей, используется чаще всего для автомобилей. Рекомендуется как грунт для двухслойных покрытий. Создан специально для жестких климатических условий России.
5. Body 425 Zinc Spot аэрозольный – однокомпонентный, быстросохнущий, антикоррозийный грунт с большим содержанием цинка.
Преимущества:
- Обладает очень хорошей токопроводящей способностью.
- Содержит акриловые синтетические и нитроцеллюлозные смолы и цинк. Не содержит хроматов свинца.
- Отличается очень удобным для руки флаконом и разбрызгивающей способностью.
- Обладает превосходной антикоррозийной защитой.
- Может окрашиваться любыми типами красок поверх нанесенного слоя.
Применяется чаще всего вовремя контактно-точечной сварки и дуговой сварки с помощью плавящегося металлического электрода в среде инертного газа.
6. CRC AC-PRIMER – грунтовка-аэрозоль с множеством функций.
Преимущества:
- Основан на ортофосфате цинка.
- Очень быстро сохнет и подходит для любых металлических поверхностей.
- Содержит модифицированные алкидные полимеры и другие антикоррозийные красящие вещества.
- Отлично борется с ржавчиной и надежно предохраняет внутренние и внешние поверхности от образования коррозии.
- Имеет светло-серый цвет, что позволяет наносить поверх него даже самые светлые краски.
- Сохнет всего лишь за час, после чего уже можно наносить финишные покрытия.
Применяется для кузовов автомобилей, заводского оборудования и механизмов, судостроительной арматуры, элементов стальных конструкций зданий, металлических окон, ходовых частей и каркасов, сварных швов и точечной сварки.
7. APP Zink 98 спрей — качественный препарат цинка длительного действия для защиты железа или стали от коррозии.
Преимущества:
- В составе более 90% чистого цинка, синтетические смолы и дополнительные защитные компоненты.
- Относится к краскам специального назначения на базе силиконовой смолы.
- Слой устойчив к воздействию воды, бензина и мелких механических повреждений.
- Выдерживает температуры до 300 градусов C.
- После высыхания слоя поверхность может быть окрашена.
Им покрывают предметы из стали и алюминия, подверженные воздействию высоких температур. Спрей отлично защищает от коррозии выхлопные системы мотоциклов, автомобилей, блоков двигателя, трубы радиаторов, а также решетки и каминные трубы.
8. Zink Spray LIQUI MOLY – цинковая грунтовка для получения матового антикоррозионного слоя, создающая длительную, эффективную защиту.
Преимущества:
- Состоит на 99% из высокоочищенного цинка для обработки поверхностей, где обычная покраска невозможна.
- Выдерживает температуры до + 400°С.
- Может быть использована для восстановления поврежденных гальванизированных поверхностей.
- Придает отличный внешний вид.
- Разрешает сварку поверх покрытия.
Liqui moly можно использовать практически везде, где требуется защита от ржавчины и коррозии. Применяется для ремонта поврежденных гальванических покрытий цинком, как грунтовка, защите частей кузова и системы выхлопа. Обеспечивает защиту от коррозии всех железных и стальных поверхностей, в особенности сварные швы.
СВЯЖИТЕСЬ С НАМИ ПРЯМО СЕЙЧАС И УЗНАЙТЕ О САМЫХ ВЫГОДНЫХ ПРЕДЛОЖЕНИЯХ, СКИДКАХ И АКЦИЯХ!
телефон: 8 (800) 707-53-17
e-mail: [email protected]
Для вас мы работаем: пн-пт 9:00-18:00
С уважением, коллектив магазина TDSPRAY.ru
ᐉ 5 лучших антикоррозийных средств для автомобиля — Рейтинг 2020 (топ 5)
8 лучших антикоррозийных средств для автомобиля
Конечно, Кентервильское привидение коррозии уже не так сильно пугает владельцев даже бюджетных автомобилей – одна только протравка фосфатирующим грунтом при окраске на заводе дает многое. Если, конечно, речь не идет об УАЗовском «Патриоте» — тот своей склонностью гнить уже на стоянке автосалона известен печально, и не зря – автору, например, хорошо знаком человек, умудрившийся успеть дважды поменять всю машину по гарантии из-за вылезавшей уже спустя полгода сквозной (!) коррозии. Но и не новых автомобилей у нас на дорогах много, да и не одними только защитными свойствами отличаются современные антикоры – многие составы имеют еще и приличные шумоизоляционные свойства, если правильно нанесены. Так что популярность антикоров все равно не особо снижается.
Но проблема в том, что разных составов и форм в автомагазинах много, и не все они либо эффективны в принципе, либо мало подходят для самостоятельного применения. Тогда что именно выбирать? Попробуем разобраться.
Рейтинг лучших антикоррозийных средств для автомобиля
Лучшие антикоры для днища
Dinitrol 479
Перед нами – очередной случай, когда репутацию хорошего, в общем-то, средства успели основательно испортить дилерские автосалоны, где его предлагают активно.
Итак, поговорим о том, как это делается правильно, и что это дает. Dinitrol 479 – состав на основе синтетической резины, совмещенный с ингибиторами коррозии. Адгезия у засохшего состава отличная – очистить тот же пистолет, забыв это сделать сразу после работы, труд адский. Правильно настроенное распыление заставляет наносимый на поверхность состав вспениваться – микропузырьки воздуха, остающиеся в застывающем антикоре, как раз и обеспечивают тому и шумоизоляционные свойства, и увеличивают стойкость к ударам гравия: слой антикора лучше демпфирует удары. И, кстати, по этой же причине аналогичные по назначению составы в аэрозольных баллончиках от этого производителя мы рекомендовать не будем – такого эффекта у них нет.
Поскольку состав очень густой, способности затекать в «узкие» места, микротрещины заводского покрытия, проникать в уже появившиеся очаги коррозии у него нет в принципе. К этому добавим чувствительность к качеству подготовки поверхности: именно поэтому Dinitrol 479 и рекомендуется в первую очередь для новых авто.
- Долговечность покрытия
- Выраженные шумоизолирующие свойства
- Требовательность к оборудованию
- Правильно работает только при вполне определенных условиях нанесения
Tectyl Bodysafe
«Встретим по одежке» — в розничную сеть Tectyl Bodysafe поставляется в литровых «евробанках» под пистолет и пятилитровых ведерках. «Оптовая» же фасовка для автосервисов – это не только 20-литровые ведра, но и бочки по 59 и 203 литра. Вязкость у состава средняя, так что особых проблем с нанесением у него нет, адгезия и проникающая способность хорошие.
Антикор отличается и хорошей долговечностью, спокойно переносит перепады температур и воздействие соли. Приличны и ингибирующие свойства, так что выбор для автомобилей, уже успевших хорошо познакомиться с отечественными дорогами, логичен. Из минусов отметим не самую высокую прочность покрытия на пробой (удары камней, например) – поэтому не стоит экономить с толщиной нанесенного антикора, использовать поверху дополнительный слой мастики или антигравия. Зато эта самая прочность не ухудшается после длительного воздействия соли и нескольких циклов заморозки, что уже радует гораздо больше.
- Высокая адгезия, приличная способность к проникновению в микродефекты
- Морозостойкость
- Минимальное изменение свойств под воздействием соли
- Не самая высокая ударная прочность
- Минимальный шумоизолирующий эффект
LIQUI MOLY Wachs-Korrosions-Schutz
Этот битумно-восковый антикоррозийный состав весьма хорош, но подводит его фасовка – только и исключительно литровые банки под пистолет. На полную обработку днища и арок такой банки не хватит и «Оке», если подходить к процессу с умом, а не пылить «чтобы было». При этом отметим, что испаряется примерно половина нанесенного состава: летучих веществ в нем много, что, с одной стороны, облегчает нанесение и делает состав более текучим до высыхания, но с другой заставляет сразу купить несколько банок. «Динитроловские» ведерки в этом плане куда практичнее.
Плюс состава – его хорошая эластичность, покрытие хорошо переносит абразивное воздействие песка, удары камней, морозы. А вот шумоизоляционными свойствами он особо не отличается, при этом пять литров состава обойдутся в те же самые деньги, что и пятилитровое ведро Dinitrol 479. Так что реальным достоинством антикора от Liqui Moly можно назвать только более легкое нанесение, и расстановка приоритетов в сегодняшнем рейтинге лучших антикоров становится очевидной.
- Простота нанесения (сойдет и дешевый пистолет из ближайшего магазина)
- Хорошая эластичность
- Стойкость к соли
- Высокая доля летучих веществ
- Фасовка только в литровые банки
- Нет ощутимых шумоизоляционных свойств
Body 930
Однако у бюджетности есть своя цена: высохший состав достаточно твердый, а это минус и к морозостойкости, и к стойкости против ударов. Рекомендовать такой антикор можно в первую очередь для автомобилей, эксплуатируемых в умеренном и теплом климате преимущественно в городе – тут он прослужит дольше. Твердого остатка достаточно много – более 60 процентов, в этом плане греки, конечно, обошли не самый удачный по «летучести» состав Liqui Moly. По шумоизоляционным свойствам этот антикор, даже будучи нанесенным толстым слоем с помощью пистолета, также оказывается в числе аутсайдеров.
Учитывая все минусы, посоветовать антикор от Body можно только при крайне ограниченном бюджете и для тех автомобилей, у которых хоть какая-то мастика нанесена на заводе.
- Низкая цена
- Простота нанесения
- Выбор фасовок до 20 литров
- Не лучшие защитные свойства
Лучшие антикоры для скрытых полостей
Dinitrol ML
Хорошо антикор выдерживает и воздействие «лужковского коктейля» на уже обработанную поверхность. Так что по совокупности свойств он и своих денег стоит, и соответствующий балл в рейтинге лучших антикоррозийных средств заслужил.
Интересный нюанс — то, что производитель рекомендует проводить двойную обработку, напыляя поверх «вставшей» пленки Dinitrol ML второй состав – Dinitrol 1000. Здесь хитрость в том, что самая сильная сторона ML – это проникновение в ржавчину, а вот толщиной слоя после высыхания он не может как раз в силу текучести. «Тысячник» же образует более толстую и прочную пленку, выступая как защитный слой. Многие производители таких рекомендаций не дают, а зря – начитавшись обещаний непревзойденной защиты, можно получить посредственный результат, не проведя дополнительную обработку поверх эффективного, но тонкого основного слоя антикора.
- Высокая проникающая способность
- Эффективные ингибирующие свойства
- «Несамостоятельность» — желательно покрывать слой Dinitrol ML дополнительным составом сверху
LIQUI MOLY Hohlraum-Versiegelung
Если учесть, что цена у обоих аэрозолей плюс-минус равна за один и тот же объем, проигрыш Liqui Moly очевиден. Но нельзя не признать хорошие водоотталкивающие свойства пленки и сохранение ей эластичности на морозе, хотя при такой толщине это и не так удивительно. В любом случае состав довольно-таки интересный, при грамотном применении покажет себя хорошо. Подойдет он и для профилактики на новой машине, и как средство оттянуть неизбежное на машине с пробегом, где коррозия в скрытых полостях уже неизбежно начала разрастаться.
- Приличная адгезия
- Стойкость к воздействию соли
- Хорошее проникновение в ржавчину
- Очень тонкая пленка после высыхания
Tectyl ML
Этот антикор – в первую очередь консервант, обработанная поверхность надолго сохраняет способность сопротивляться воде и соли. Но, если нужно уже не предотвращать, а бороться со ржавчиной, то стоит обратить внимание на другой спрей с таким же названием – Dinitrol ML. Который к тому же еще и дешевле. А говоря именно о составах с выраженным «консервирующим» характером, то вновь можно задуматься – не купить ли тогда уж Dinitrol 1000?
- Отличная адгезия
- Прочность пленки
- Эффективное противодействие попадающей снаружи влаге и соли
- Недостаточная глубина проникновения в ржавчину
ВЭЛВ Мовиль-5Э
Проникающая способность у этого антикора не лучшая – он эффективно «консервирует» только начинающую разрастаться ржавчину. Выталкивает воду из микропор он тоже не так чтобы хорошо, в итоге в крупном очаге коррозии фактически образуется сырой и соленый «парник» под слоем антикора. Результат ожидаем. Длительное воздействие противогололедным реагентам – за этим тоже не к «Мовилю-5Э».
Поэтому, не отрицая высокие гидрофобные свойства (еще бы – состоит то мовиль по оригинальному рецепту в основном из масла и олифы), дешевизну и простоту нанесения, высокий балл мы поставить никак не можем: современные составы долговечнее и эффективнее.
- Низкая цена
- Простота нанесения
- Безвредность для краски
- Неизбежное стекание
- Не лучшее проникновение в ржавчину
Какой антикор выбрать?
Основных применений у антикоррозийных средств два, соответственно и требования к обоим группам очень сильно различаются.
Антикоры для днища и колесных арок подвергаются постоянному абразивному воздействию песка и ударам. Поэтому от них требуется сохранение высокой прочности. В идеале антикор для днища должен обладать выраженными тиксторопными свойствами – то есть твердая пленка, надежно противостоящая истиранию, обдиранию жесткими ветками и прочим, что может попасть под днище, в точке удара как бы «разжижается», гася энергию удара, а не растрескиваясь или скалываясь. Такой антикор надежно защитит днище на долгое время.
Стойкость к соли очень важна – зимой днище и арки будут обрастать слоем дорожной грязи, то есть противогололедные реагенты будут действовать на покрытие очень длительное время. Разрушающийся в подобных условиях антикор надолго машину не защитит.
Такие антикоры в основном рассчитаны на нанесение специальными пистолетами для высоковязких составов. Это позволяет быстро наносить слой нужной толщины, вспенивать его для улучшения шумоизоляции. Но проникает в микропоры и ржавчину густая мастика очень плохо – то есть наносить подобный состав нужно либо на чистое, еще не имеющее повреждений днище нового автомобиля, или предварительно удалить либо обработать химически имеющиеся следы коррозии.
А вот антикоры для скрытых полостей, наоборот, очень текучи – их задача проникать в самые труднодоступные места, ведь глазами проконтролировать нанесение антикора, в отличие от обработки днища, тут проблематично. Текучесть позволяет антикорам для скрытых полостей отлично проникать и в трещины, микропоры краски, пропитывать ржавчину – поэтому в их состав можно вводить очень эффективные ингибиторы коррозии. Но и высыхать антикор должен быстро, оставляя прочную пленку – иначе, стекая вниз, как «Мовиль» или тот же «Раст-стоп», он будет со временем все больше «оголять» защиту.
Хорошо подготовить скрытые полости к обработке нелегко – это не днище, которое хоть пескоструем можно драть до чистого металла. Поэтому к антикору предъявляются еще и высокие требования по вытеснению воды, солевых растворов – проникая в микротрещины и ржавый слой, антикор обязан вытеснить причину коррозии, а не «запечатать» ее собой, иначе металл продолжит гнить.
В любом случае не забывайте о прочтении инструкции и о качестве подготовки: ничто так не портит результат антикоррозийной обработки, как несоблюдение требований производителя к применению антикора или грубые ошибки в подготовке автомобиля.
Автомобиль – это не просто средство передвижения, а железный друг. В нём можно переждать ссору с женой или просто побыть в одиночестве, уехать в другой город. Но пока владелец проводит остальное время под крышей дома своего, автом
Рейтинг ТОП 7 лучших антикоррозийных средств для автомобиля
ОБЛАСТЬ ПРИМЕНЕНИЯ
Mercasol 3 / 3 AL является разновидностью одного материала, отличающаяся цветом, предназначен для индивидуальной антикоррозионной обработки в гаражах или мастерских. Используется для внутренних полостей, порогов и соединений на автомобилях для защиты от гравия и коррозии. Mercasol 3 / 3 AL может использоваться вместе с препаратами Mercasol 1, нанесенным ранее. Mercasol купить и нанести можно самому не прибегая к услугам автосервисов.
ХАРАКТЕРИСТИКИ
Mercasol 3 / 3 AL — черного и бронзового цвета соответственно. Mercasol 3 / 3 AL является хорошим проникающим антикор. средством с содержанием растворителя (алифатические нафтены) на воско-масляной основе. Обладает хорошими антикор. свойствами в течение длительного периода времени. Создает пленку для защиты от гравия. Препарат был протестирован на совместимость с наиболее распространенными антикор. системами на рынке и одобрен для применения на большей части различных марок автомобилей.
ПОДГОТОВКА ПОВЕРХНОСТИ
Обрабатываемая поверхность должна быть сухой и очищенной от грязи, соли и масел. Возможно использование Меркасола 1 перед нанесением Mercasol 3 / 3 AL.
НАНЕСЕНИЕ
Нанесение должно производиться в помещении при температуре от +15ºС — +40ºС. Mercasol 3 / 3 AL должен наноситься безвоздушным методом или воздушным методом с использованием оборудования Гевеко.
Аэрозоль Mercasol 3 / 3 AL можно также наносить распылением через установленный на баллоне носик.
РЕКОМЕНДУЕМАЯ ТОЛЩИНА СЛОЯ
200 мкм толщина влажного слоя дает толщину 90 мкм сухого слоя. Возможно повторное нанесение для получения более толстой пленки.
РАСХОД МАТЕРИАЛА
ОЧИСТКА
Очистка оборудования проводится алифатическим растворителем. Излишки материала предпочтительнее удалять препаратом Mercasol Cleaner или алифатическим растворителем.
ВРЕМЯ ВЫСЫХАНИЯ
Время высыхания зависит от температуры и влажности, при температуре +23ºС и относительной влажности 50% время высыхания составляет приблизительно 4 часа.
ХРАНЕНИЕ
Срок хранения – 12 месяцев, при соблюдении соответствующей инструкции.
ТЕХНИЧЕСКИЕ ДАННЫЕ
- Слой Восковой
- Проникающая Способность >70 мм в полости 50 мкм
- Адгезия при Отсутствие трещин и низкой температуре отслаивания при температуре -20ºС
- Растворитель Алифатические нафтены
какая лучше, особенности выбора, виды, применение и отзывы
В процессе эксплуатации автомобилей следует регулярно обрабатывать кузов от коррозии. При движении гравий и небольшие камни медленно, но верно разрушают ЛКП бамперов и крыльев. В эти царапины попадает влага, и со временем запускаются коррозионные процессы. Автолюбители задаются вопросом о том, какой антикор лучше. Попытаемся выяснить это.
Обрабатывать или нет?
Средства для борьбы с коррозией предназначены для обработки днища автомобиля, прочих кузовных деталей. Некоторые автовладельцы не обрабатывают свои автомобили. У них на это есть различные причины: кто-то уверен, что это пустая трата денег, другие считают, что машина отслужит свой срок без вмешательства. Однако отзывы автолюбителей говорят, что материалы для борьбы с коррозией работают и применение их оправдывается.
Даже самые лучшие антикоррозийные средства для автомобиля не идут ни в какое сравнение с новым авто. Если машина эксплуатируется в неблагоприятных условиях, когда на металл кузова воздействуют перепады температур, проблемы с ЛКП могут появиться уже на 3 году использования. Однако отзывы говорят, что мастики и прочие антикоры препятствуют возникновению трещин и ржавчины.
Антикор – что это?
Антикоррозийные препараты представляют собой специальные составы, которые необходимо наносить на кузовные детали и скрытые полости. Эти средства не позволяют развиться ржавчине на металлических поверхностях. Средства, которыми сегодня обрабатывают автомобили, можно разделить на:
- Смеси на основе восков.
- Битумные составы.
На базе этих препаратов сегодня производят огромное количество различных антикоррозийных продуктов для авто. В составе, кроме этих компонентов, могут быть вещества, повышающие эффективность препарата. К примеру, в восковых продуктах присутствуют добавки, увеличивающие прочность металла и замедляющие коррозионные процессы. В битумные составы включены металлические смеси.
Большой популярностью у опытных автомобилистов пользуются продукты на основе полимеров и парафинов. Дополнительно в составе находятся различные смеси резины, каучуков и пластиков. Во все препараты добавляют не только вещества, защищающие ЛКП от ржавчины, но и те, функция которых – выталкивать влагу.
Коррозионные процессы бывают двух видов: химические и электрохимические. В первом случае коррозия возникает за счет воздействия на кузов кислорода и соединений, которые его содержат. В процессе электрохимического воздействия кузов находится в контакте с электролитами. В зависимости от типа ржавчины делается вывод, какой антикор лучше выбрать для авто.
Как выбирать антикоррозийные препараты?
Все существующие на рынках автомобильной химии средства классифицируются по различным факторам. Это особенности нанесения, химический состав смесей, место нанесения. Есть разная антикорозийка для авто. Какая лучше? Только та, которая подходит в конкретной ситуации.
Битумные мастики изготавливаются на основе разнообразных смол. Этот состав решает две важнейшие задачи – защищает всю поверхность кузова автомобиля от любого механического воздействия и дополнительно выполняет функцию консервации металла. Наносить эти смеси рекомендуется слоем от 250 до 400 мкм.
Каучуковые материалы и средства на основе ПВХ считаются одними из самых долговечных среди тех, что встречаются сегодня. Применяются данные решения преимущественно на заводах.
Жидкий пластик также считается средством для антикоррозийной обработки, но его не стоит использовать в качестве основного препарата. Этот продукт не имеет необходимой механической стойкости.Все эти решения подходят и используются только для обработки внешних кузовных деталей и частей, которые находятся в свободном доступе. Но это далеко не все поверхности, которые подлежат обслуживанию – автомобили имеют массу скрытых полостей. Для обработки таковых следует применять другие продукты.
Так, для скрытых мест подойдет масляная антикорозийка для авто. Какая лучше среди них? Только та, которая изготовлена на основе невысыхающих масел. Жидкие антикоррозийные средства находятся именно в таком состоянии и после нанесения, а также в процессе эксплуатации машины. Препараты такого плана хороши тем, что они заполняют собой все трещины и царапины на поверхности металла.
Продукция на парафиновой основе изготавливается преимущественно из восков. Когда состав застынет, он превратится в тонкую эластичную пленку. Данное решение среди прочих достоинств отлично сохраняет свои эксплуатационные качества даже при низких температурах.
Антикорозийка для автомобиля: какая лучше?
Те автомобилисты, которые впервые в жизни столкнулись с коррозионными процессами на поверхности кузова, часто не знают, что выбрать среди массы предложений рынка. К любому средству, защищающему металл от ржавчины, предъявляются определенные требования. Их необходимо знать, прежде чем совершить покупку какого-либо препарата.
Продукты для применения в скрытых полостях не должны воздействовать на лакокрасочное покрытие. Также качественное средство имеет высокую адгезию и однородную структуру. Кроме того, желательны высокие проникающие способности – смесь должна попадать везде, вне зависимости от того, есть коррозия или ее нет.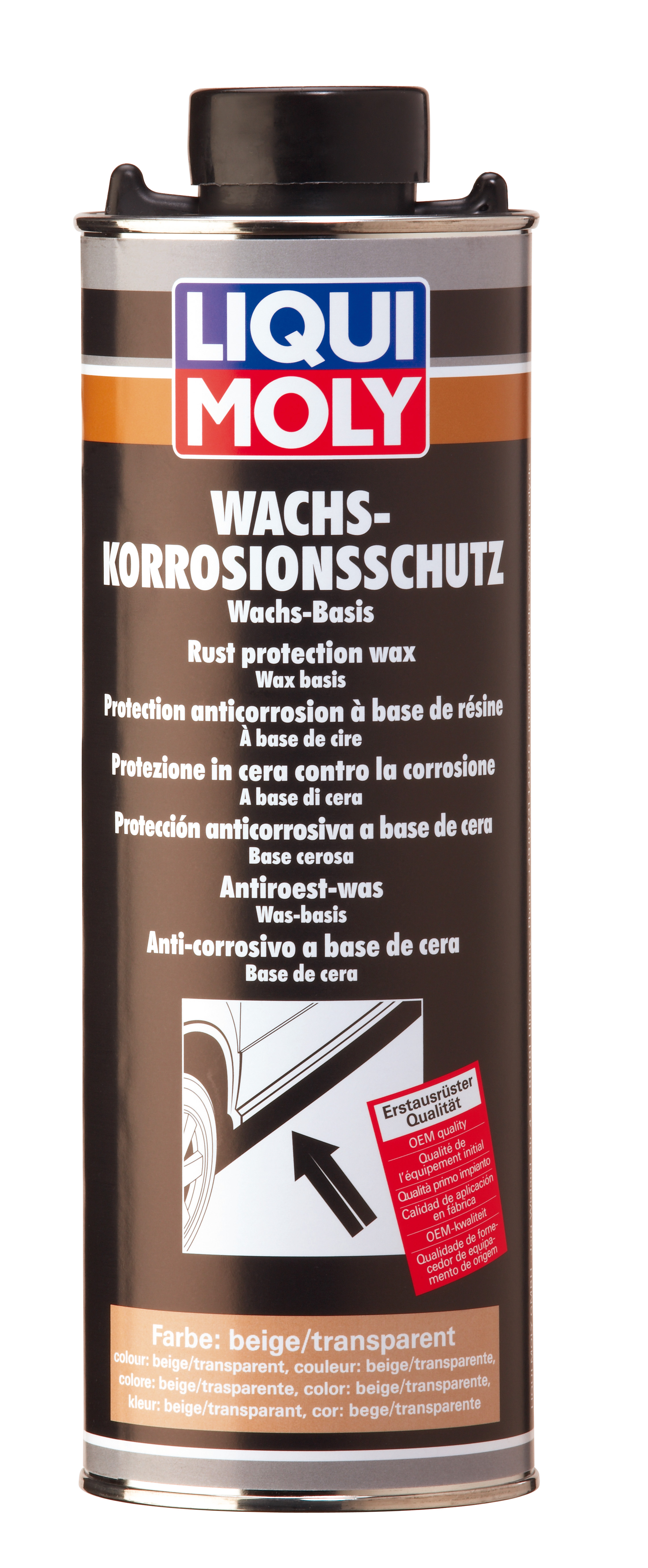
Здесь нельзя сказать, что нужна какая-то конкретная антикорозийка для авто. Какая лучше, не скажут даже опытные специалисты – выбрать из предлагаемого ассортимента подобной химии универсальное средство на самом деле практически невозможно.
Составы для внешних поверхностей должны защищать металл кузова от воздействия электролитов. Еще одно требование – хорошая адгезия, устойчивость к механическим воздействиям и деформации железа.
Тем, кто хочет знать, какой антикор лучший для авто, советы мастеров автосервисов помогут. Профессионалы утверждают, что лучшим препаратом можно считать только то средство, которое максимально отвечает всем вышеперечисленным требованиям. Продукты известных брендов могут стоить достаточно дорого, поэтому рекомендуется выбирать оптимальный по качеству и цене материал.Сегодня в продаже появились специальные смеси для нанесения на пораженные коррозией места. Указанные препараты преобразовывают ржавчину – в составе есть кислота. Этим средством рекомендуется пользоваться, когда выполняется начальная подготовка к покраске. Ржавчина превращается в пленку, которую нет необходимости удалять.
Мастики для авто
Сегодня на рынке есть несколько наиболее популярных и эффективных материалов для борьбы с ржавчиной. Что лучше? Выбор зависит от свойств препарата и от мест, где кузов поврежден.
Мовиль
Мовиль способен надежно защитить кузовные детали от коррозионных процессов. Он также подходит для обработки мест, где детали соединяются. Отзывы говорят, что этот материал также эффективно вытесняет влагу и образует восковый слой с высокими характеристиками.
Мовилей существует огромное количество, и все они подходят для применения. Используются и как антикор для обработки нового автомобиля. Какой выбрать? Надо делать вывод, исходя из требований и стоимости.Битумно-каучуковые мастики
Применяются для нанесения на внешние, а также внутренние поверхности кузова автомобилей. Обрабатывать этими мастиками можно салон, крылья и багажник.
Сланцевые мастики
Зачастую применяются для нанесения на днище и колесные арки. После застывания образуется прочная битумная пленка, которая обеспечивает надежную гидроизоляцию.
Резинобитумные мастики
Эти решения можно применить для днища и колесных арок. Отзывы говорят, что данный препарат устойчиво выдерживает перепады температуры. Данными смесями можно обрабатывать внешние и внутренние детали. Защитный слой отличается высокой эластичностью и устойчивостью. Эти препараты подойдут для зимней эксплуатации.
Лучшие препараты
Стоит обратить внимание на продукцию немецкого бренда Dinitrol. Продукт отличается высокими характеристиками и качественной адгезией. Покрытие может затягивать неглубокие царапины. Эта хоть и дорогая, но качественная антикорозийка для авто. Какая лучше? Многие владельцы авто считают, что именно эта. Следует обратить внимание на состав и цену. Стоит она от 660 р за 500 мл.
А если нужно бюджетное средство, то подойдет продукт от RunWay.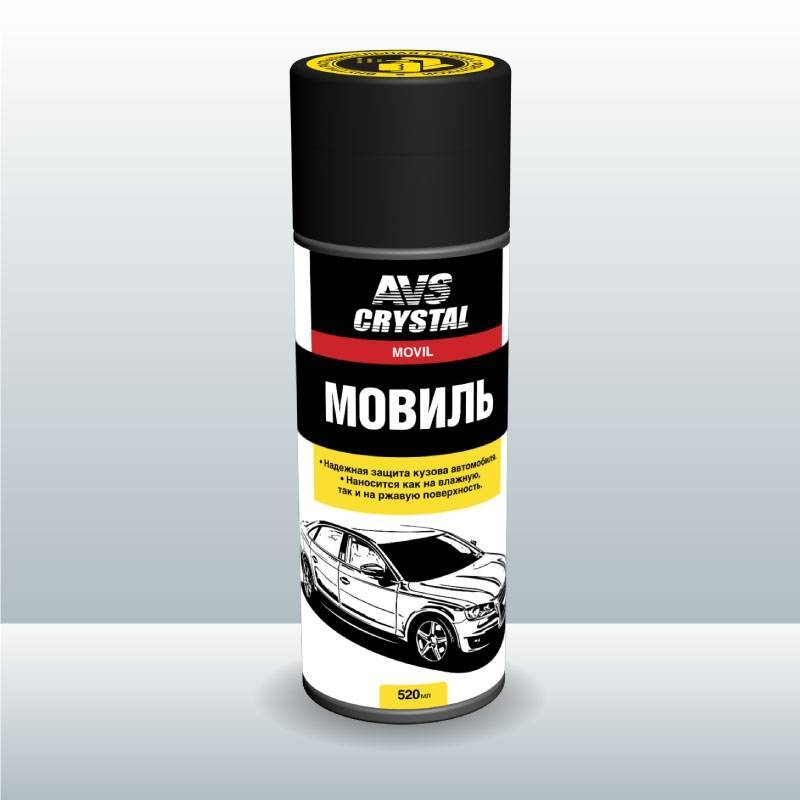
Каждому автомобилисту иногда просто необходима антикорозийка для авто. Какая лучше цена для нее – стоит выбирать в зависимости от состояния автомобиля. Минимальная стоимость отечественной продукции – 200 р., а максимальная цена на импортные препараты может достигать нескольких тысяч.
сравнение, классификация и рекомендации по выбору
Чтобы нейтрализовать воздействие негативных внешних факторов и остановить появление коррозии, для автомобиля разработали множество защитных средств, которые принято называть «антикорами». Ниже мы поговорим о том, что такое антикор автомобиля и какая лучше антикоррозийка для авто.
Чтобы защитить кузов и остальные части авто от коррозии, его покрывают лакокрасочным слоем – он создаёт непроницаемую плёнку, которая препятствует возникновению ржавчины. Однако со временем герметичность лакокрасочного покрытия нарушается – это происходит даже при самой аккуратной эксплуатации авто. Причиной тому самые разные факторы, среди которых:
- внешние механические воздействия;
- влияние атмосферных факторов;
- присутствие на дороге в большом количестве химически активных реагентов;
- абразивное воздействие мелких твёрдых частиц в потоке встречного воздуха и т. п.
В результате воздействия перечисленных факторов на лакокрасочном слое появляются трещины, царапины и сколы – металл в этих местах остаётся без защиты, и создаются положительные условия для появления очагов коррозии.
Смотрите также:
Определение антикоррозийного средства
Антикор – это специальное вещество, которым покрывают участки, наиболее подверженные появлению очагов ржавчины. К таким местам относят днище, арки колёс и т. п. Принцип, по которому действует антикоррозийка для авто, достаточно прост – она создаёт плотную плёнку, защищающую машину от появления ржавчины.
Существует две основные группы таких средств – одна из них изготавливается на битумной основе, вторая – на основе различных восков. Кроме этого, разработали множество разнообразных добавок, которые делают средство более эффективным: увеличители прочностных характеристик металлов, замедлители коррозионных процессов, металлические смеси и т. п. Широко распространена группа материалов с основой из полимеров или парафина с резиновыми, каучуковыми и пластиковыми присадками.
Практически любая антикоррозийка для авто обладает гидрофобными характеристиками – она отталкивает влагу, не давая ей задерживаться после мытья машины или попадания под дождь. У новичков часто возникает вопрос: какой антикор для авто лучше и какой антикор выбрать? Чтобы получить ответы на эти вопросы, следует для начала разобраться в классификации и особенностях применения различных видов.
Смотрите также:
Классификация
В зависимости от химического состава и специфики применения, антикоррозийные средства для автомобилей делят на несколько категорий. Прежде чем решить, какой антикор для авто лучше, следует внимательно изучить, что сообщает инструкция о его особенностях.
Решая, какая антикорозийка лучше, прежде всего учитывайте, что средства различаются по разным параметрам, один из которых — место их примененияПо химическому составу такие средства делятся на следующие категории:
- битумные мастики – их изготавливают из синтетических смол, они предназначены для того, чтобы защищать поверхность машины от внешних механических воздействий, а также, таким образом, обеспечивается консервация металлических поверхностей. Толщина нанесения битумной мастики составляет 250–400 микрометров;
- вещества на поливинилхлоридной и каучуковой основе – они наиболее долговечны и надёжны.
Применяют эту категорию, как правило, в заводских условиях;
- жидкий пластик – рекомендуется использовать его как дополнительное средство, поскольку он не характеризуется надёжностью и долговечностью;
- невысыхающие масляные составы – они остаются в жидком состоянии на протяжении всего срока эксплуатации. Отличаются хорошей заполняемостью, консервируя все поры и трещины в материале.
- парафиновые и восковые составы – образуют эластичную плёнку, защищающую поверхность от образования ржавчины. Показали высокую стойкость к сильным перепадам температуры.
Водителям, определяющим, какой антикор для авто лучше, следует знать, что первые три категории применяются для защиты внешних поверхностей, доступ к которым не представляет особых трудностей. Две последние разновидности используют для обработки труднодоступных участков автомобиля.
Смотрите также:
Требования к антикоррозийным средствам
Прежде чем решать, какой антикор лучше, рекомендуется разобраться в требованиях, которые выдвигаются к таким средствам. Чтобы иметь основания считать, что антикоррозийка подходит для скрытых участков авто, она должна отвечать следующим требованиям:
- не наносить вреда лакокрасочному слою на кузове автомобиля;
- характеризоваться хорошей адгезией и давать покрытие с однородной структурой;
- хорошо заполнять все микротрещины и микропоры, а также участки с очагами ржавчины;
- иметь высокие гидрофобные характеристики, чтобы влага, попадающая на различные участки машины, не задерживалась и оперативно удалялась;
- прежде чем выбирать, какой антикор для авто лучше, поинтересуйтесь, насколько долговечно покрытие из него.
Средства для легкодоступных и открытых участков автомобиля должны отвечать следующим требованиям:
- сглаживать воздействие электролитов на металлические части кузова машины;
- обладать хорошими адгезивными свойствами;
- иметь высокие показатели эластичности, чтобы не терять целостности в случаях деформаций кузова;
- не разрушаться под воздействием ударов щебёнки и мелких камней, вылетающих из-под колёс проходящих рядом машин.
Оценивая перечисленные критерии, можно принять решение, какой антикор для авто лучше в том или ином случае.
Смотрите также:
Выбираем антикоррозийку для машины
Принимая решение, какой антикор лучше купить для своей машины, следует понимать, что ни один специалист не сможет вам порекомендовать универсальное средство, которое идеально подойдёт для любых задач. Многообразие видов антикоррозийных средств объясняется тем, что водителям дают возможность эффективно организовать защиту своей машины с учётом её особенностей.
Эффективно вытесняя влагу, образует слой воска, имеющий отличные проникающие характеристикиНиже мы приводим несколько распространённых средств и показаний к их применению – возможно, эта информация окажется полезной при выборе антикоррозийки:
- Мовиль – это вещество с высокой проникающей способностью отлично избавляет машину от лишней влаги и защищает её от ржавчины. В результате обработки образуется эластичный восковый слой, который надёжен и долговечен.
- Битумно-каучуковые мастики – их обычно используют для тех мест авто, где нет лакокрасочного покрытия, а также пола в салоне, багажника, крыльев и т. п.
- Сланцевые мастики – их выбирают для днища и наружных поверхностей колёсных арок. Битумное покрытие гидроизолирует металл и защищает его от ржавчины.
- Резинобитумные мастики хорошо «работают» при сильных температурных перепадах и отлично показали себя при обработке наружных и внутренних частей машины. Эластичный слой хорошо держится даже в самые сильные морозы, не трескаясь и не отслаиваясь.
- Пороговый антиоксидант подходит для того, чтобы защитить двери, стойки и т.п. Если речь идёт о скрытых участках, рекомендуется предварительно их обработать консервантом, который не боится коррозии и противостоит воздействию влаги.
Производят на основе смол, защищает поверхность от механических воздействий, обладает свойством консервировать металл
- В качестве антикоррозийки некоторые водители применяют антигравий – его наносят на кузов, бампер, пороги и т.
п. Он защищает машину от ударов щебёнки и истирающего воздействия мелких песчинок. Такие вещества делают на основе каучука, дающего прочную эластичную плёнку.
- Антикор по ржавчине – он превращает ржавчину в специальную плёнку, не дающую коррозии распространяться дальше. Использование этой разновидности избавляет вас от зачистки проблемных участков с появившимися признаками корродирования.
Преимущества использования антикоррозийки
Некоторые водители утверждают, что использование антикоррозийных составов не имеет практической пользы, становясь источником неоправданных финансовых расходов. Можно также услышать мнение, что не следует вмешиваться в естественные процессы, давая автомобилю отработать тот срок, на который он рассчитан.
Это ошибочный подход, поскольку применение антикоррозийки даёт следующие преимущества:
- расходы на антикоррозийную обработку гораздо ниже, чем затраты на ремонт или покупку нового автомобиля;
- если вы эксплуатируете машину в неблагоприятных условиях, признаки коррозии могут появиться уже через три года.
Вряд ли такой срок службы машины является естественным – большинство водителей надеется на многолетнюю эксплуатацию;
- процедура прохождения техосмотра автомобилем, обработанным антикоррозийкой, гораздо проще – это может подтвердить любой владелец авто, который с этим сталкивался.
Описанные средства помогают заботиться об автомобиле без лишних трудностей, потерь времени и значительного ущерба для бюджета. Современный автомобиль рассчитан на то, что водитель будет относиться к нему бережно и соблюдать требования по правильной эксплуатации. А они включают в себя обработку машины антикорозийными веществами.
[democracy]
[democracy]
Автор: Семин Виктор Юрьевич
Образование: Самарский автодорожный колледж. Инженер телекоммуникаций и электроники. Водитель второй категории/автослесарь. Навыки ремонта машин отечественного производства, ремонт ходовой, ремонт тормозной системы, ремонт коробок передач, кузовные…
Антикор авто
• Подготовка (разборка, мойка, осмотр, сушка, зачистка, маскировка)
• Обработка скрытых полостей нижней части — основания кузова (лонжероны, пороги, усилители пола, швы, полые кронштейны подвески, поперечные балки)
• Обработка днища, колесных арок (покрытие днища, колесных арок, антигравий, «жидкие подкрылки»)
• Обработка скрытых полостей верхней части кузова (двери, стойки, усилители капота, багажника, швы, уплотнители, молдинги)
• Сборка, мойка (контроль покрытия, снятие маскировки, установка снятых деталей, удаление попавших на ЛКП антикоррозионных материалов, финальная мойка кузова, протирка стекол)
1. Подготовка
— Автомобиль устанавливается на подъемник, снимаются колеса,
— демонтируются подкрылки, брызговики, защитные кожухи…
— Кузов тщательно промывается водой под высоким давлением…
— затем, наносятся моечные растворы…
— выдержав некоторое время, чтобы дать химии поработать, растворы смываются…
— В процессе антикоррозионной обработки, подготовка это одна из важнейших (и наиболее длительных по времени) составляющих, поэтому мойке уделяется большое внимание.
— Отдельно моются кожухи, подкрылки и т. д.
— Затем кузов сушится. Чаше это делается с применением тепловых пушек.
Например, при использовании тепловых пушек мощностью 25 -30 кВт, и потоком воздуха около 3000 куб. м/час, это занимает от 3 до 5 часов.
Перед сушкой нужно убедиться, что с дренажных отверстий удалены заглушки.
— в процессе сушки, кузов также продувается сжатым воздухом.
Это делается с целью ускорения процесса сушки, а также что бы выгнать воду из швов, пазух, карманов и дополнительной прочистки труднодоступных мест, которые не промылись при мойке.
— просушенный кузов тщательно осматривается для определения состояния защитных покрытий и общего состояния кузова (наличие коррозии, деформаций, повреждений, отслоений защитных и декоративных покрытий и т. д.)
…визуально…
…, с помощью бороскопа…
— Далее укрываются детали, не подлежащие обработке (тормозные механизмы, двигатель, выхлопная система, некоторые элементы подвески…)
При маскировке нужно обратить внимание на датчики АБС, кислородные датчики на выпускной системе, радиаторы, различные электрические разъемы.
2. Обработка скрытых полостей основания
образец схемы обработки (PDF формат)
Определяются точки обработки (на большинство автомобилей существуют рекомендованные производителем схемы обработки с указанием точек распыления)
— Снимаются резиновые, пластиковые заглушки, в некоторых случаях, при невозможности доступа через существующие отверстия, сверлятся дополнительные отверстия, при сверлении необходимо использовать специальные сверла, которые не дают стружки, могущей попасть внутрь детали.
— Далее обрабатываются скрытые полости основания кузова (пороги, лонжероны, поперечные балки, полые кронштейны подвески, усилители пола,…).
Антикоррозийная обработка скрытых полостей автомобиля производится, так называемым МЛ-методом: внутрь детали вводится специальная насадка и под давлением распыляются МЛ материалы: проникающие составы, пропитывающие сварные швы и формирующие на внутренней поверхности детали защитную пленку.
3. Обработка днища и арок колёс
Далее производится нанесение износоусточивых покрытий, так называемые «жидкие подкрылки», на подверженные абразивному воздействию детали (колесные арки, нижние полки лонжеронов, нижние продольные швы порогов и т. д.)
Основной слой наносится либо распылителем, либо кистью или шпателем, а затем подравнивается распылителем, для получения более гладкой поверхности.
В некоторых случаях, на лицевые поверхности наносят полимерные защитные материалы, так называемый «антигравий»
Далее производится антикоррозийная обработка днища автомобиля. Чаще всего, материалы на днище наносят безвоздушным распылением, под высоким давлением. На большинстве антикор центров, для обработки днища применяют насосы с пневмоприводом, для высоковязких материалов, с коэффициентами гидравлического усиления 26-50 единиц, что позволяет создать давление на выходе (в форсунке распылителя) до 400 атмосфер.
Иногда, поверхности днища, колесных арок покрывают теми же МЛ-материалами, которыми обрабатываются скрытые полости. Такая обработка очень эффективна, но недолговечна, МЛ составы имеют невысокую механическую прочность и, грубо говоря, «смываются» с днища. Это делается в случаях, когда кузов имеет серьезные коррозионные повреждения (послойная, сквозная коррозия) и есть сомнения, что удастся подготовить поверхности для нанесения полноценных долговременных покрытий.
— устанавливаются на место подкрылки, кожухи, брызговики…
— снимается маскировка…
— устанавливаются на место колеса…
— Машина опускается на пол для проведения антикоррозийной обработки скрытых полостей верха кузова (стойки, двери, усилители капота, багажника, швы и усилители моторного отсека, уплотнители…)
— Из машины вытаскивается все лишнее….
— Для предотвращения попадания материалов на обивки салона, сиденья, переднюю панель, салон укрывается чехлами
4. Обработка скрытых полостей верха кузова
Далее, используя различные насадки (МЛ-метод) обрабатываются полые детали верхней части кузова (двери, стойки, усилители капота, багажника, уплотнители, швы и усилители моторного отсека, молдинги,…)
— усилители капота…
— коробчатые, полые профили, швы и усилители моторного отсека…
— уплотнители, молдинги…
— усилители крышки багажника…
— швы, полые профили, усилители багажного отсека…
— стойки, двери, уплотнители…
5. Сборка и удаление попавших на кузов антикоррозионных материалов

— Проверяется плотность посадки резиновых уплотнителей проемов дверей, багажника, удаляются оставшиеся маскировочные материалы.
— кузов протирается специальным раствором от попавших на кузов материалов, возможно удаление, попавших на лакокрасочное покрытие антикоров уайт-спиритом. Не рекомендуется применение сильных растворителей.
— оформляется сертификат, с указанием даты, фамилий мастеров, использованных материалов, периодичностью гарантийных осмотров, рекомендаций.
6. Эксплуатация автомобиля после обработки
— После обработки желательно не ездить на машине в течение нескольких часов.
— Далее, в течение суток положен щадящий режим эксплуатации.
— Рекомендуется избегать высоких скоростей, езды по грунтовым дорогам, буксования, при проезде луж нужно снижать скорость.
— Два-три дня не рекомендуется мыть машину.
-Так же после обработки в течение пары недель, желательно, не мыть днище, арки под высоким давлением.
наверх страницы
cоставлено: Антикор.рф, г. Москва.
Защита от коррозии автомобильных деталей и безопасность
Ранее в этом году NACE International опубликовала исследование «Международные меры по предотвращению, применению и экономике коррозионных технологий» (IMPACT). По его оценкам, глобальная стоимость коррозии составляет 2,5 триллиона долларов, что составляет примерно 3,4% мирового ВВП.
Исследование также включало тематическое исследование управления коррозией в автомобильной промышленности и подчеркивало его успехи.Исследование показало, что автомобильная промышленность экономила 9,6 млрд долларов или 52% ежегодно в 1999 году по сравнению с 1975 годом, добавив, что успех был обусловлен «принятием решений по предотвращению коррозии на самом высоком уровне».
За прошедшие годы был достигнут значительный прогресс, но коррозия остается дорогостоящей проблемой для автомобильной промышленности, и недавние отзывы только высветили эту проблему.
Отзыв из-за коррозии
Полную стоимость отзыва сложно измерить количественно и варьируется в зависимости от конкретного случая.Ремонт, судебные издержки и ущерб имиджу бренда — все это может иметь финансовые последствия, которые будут во многом зависеть от дефекта, вызвавшего отзыв, и от того, как с ним бороться.
Коррозия — долгосрочная проблема для производителей автомобилей, не в последнюю очередь потому, что ряд факторов, некоторые из которых находятся вне контроля производителей оригинального оборудования, вносят свой вклад. Важнейшие детали, такие как компоненты тормозов и подвески, могут быть подвержены коррозии, и поскольку они имеют решающее значение для безопасности на дороге, производители и поставщики продолжают разрабатывать сложные технологии предотвращения коррозии.Несколько недавних отзывов, касающихся Mazda, Toyota, Kia и Mitsubishi, подчеркивают проблему коррозии деталей подвески.
В августе 2016 года Mazda подтвердила, что отзывает более 190 000 кроссоверов CX-7 с 2007 по 2012 модельные годы. Национальное управление безопасности дорожного движения США подтвердило, что вода может попасть в шарниры шарнира передней подвески CX-7. Если вода содержит загрязнители, например соль, используемую для удаления льда с дорог, это может вызвать коррозию шарового шарнира.Если коррозия была достаточно серьезной, это, в свою очередь, могло привести к отделению переднего нижнего рычага подвески от автомобиля, что затруднило управление автомобилем и увеличило риск аварии.
[inlinead]
Этим летом Toyota инициировала аналогичный отзыв: более 370 000 автомобилей Toyota и Lexus были отозваны для устранения серьезной проблемы с подвеской. Речь идет о кроссовере RAV4 2006-2011 годов и седане Lexus HS 250h 2010 года выпуска. Проблема в том, что контргайки на рычаге задней подвески могли быть неправильно затянуты.В результате они могут быть слишком ослаблены, что приведет к ржавчине резьбы и поломке рычагов подвески. Опять же, это затрудняет управление автомобилем и увеличивает риск аварии.
Еще один отзыв был произведен компанией Mitsubishi: более 174 000 автомобилей были отозваны из-за возможной коррозии передних нижних рычагов управления. Как и в случае с Kia, отзывы производятся в штатах, которые используют соль для удаления льда с дорог. Вызванная коррозия может привести к отсоединению переднего нижнего рычага подвески от других компонентов подвески, что сделает управление автомобилем небезопасным.Все отозванные автомобили будут проверены, и на новые и существующие детали будут нанесены дополнительные антикоррозионные покрытия для защиты в будущем.
Проблемы с коррозией
Отзыв является неотъемлемой частью индустрии массового производства, и, как уже упоминалось, автомобильная промышленность добилась больших успехов за предыдущие десятилетия. Однако очевидно, что коррозия все еще остается проблемой, особенно когда соль соединяется с водой, чтобы повредить металлические части и компоненты. Тот факт, что различные типы коррозии влияют на автомобили, также означает, что требуются различные решения.
Атмосферная коррозия может возникнуть при контакте любой металлической поверхности автомобиля с воздухом, содержащим влагу. Тонкой пленки влаги, осаждающейся в условиях ненулевой влажности, достаточно, чтобы вызвать постепенное разложение стальных поверхностей. Толщина пленки будет зависеть от таких факторов, как температура и давление окружающей среды, относительная влажность и присутствие солей.
Щелевая коррозия — это электрохимические процессы, происходящие в замкнутых пространствах, таких как прокладки, уплотнения, фланцы и пространства, заполненные отложениями.Этот тип коррозии — это локальное поражение из-за наличия застоявшегося раствора или электролита.
Гальваническая коррозия возникает, когда два разных металла находятся в электрическом контакте. Один металл может подвергаться коррозии преимущественно по сравнению с другим. Одним из таких примеров является коррозия гаек и болтов, соединяющих компоненты вместе.
Точечная коррозия — это еще одна форма локального воздействия, похожая на щелевую коррозию. Обычно это происходит в пассивных материалах, где пассивная оксидная пленка, которая защищает металл, разрушается в результате химического или механического воздействия.Хлор в соленой воде очень эффективно разрушает такие пассивные оксидные пленки.
Средства и решения для защиты от коррозии
Условия окружающей среды могут играть значительную роль в коррозии, но причины также могут быть связаны с производственными процессами, а обработка сама по себе является значительным сектором. Объем рынка антикоррозионных покрытий составил 22,45 млрд долларов в 2015 году и, по прогнозам, достигнет 30,04 млрд долларов к 2021 году. В отрасли существует множество решений, и некоторые из ведущих защитных покрытий подробно описаны ниже.
Henkel
Поставщик автомобильной продукции Компания Henkel предлагает ряд технологий обработки поверхностей для защиты от коррозии, включая предварительную обработку, оборудование для управления технологическим процессом, нанесение металлических покрытий и обработку поверхностей автомобилей с защитой от коррозии. Решения Henkel оптимизированы для работы с различными приложениями и процессами, от шасси до кузова в белом.
Покрытие Bonderite (ранее Aquence) M-PP 937, например, обеспечивает защиту от коррозии для таких применений, как рамы автомобилей и компоненты шасси.Эпоксидно-акриловое уретановое покрытие обеспечивает высокий блеск, сохраняя при этом высокие характеристики при испытаниях в нейтральном солевом тумане (NSS) и испытаниях на циклическую коррозию OEM. Твердое покрытие обеспечивает производителям ряд преимуществ, включая экологическую устойчивость с очень низким содержанием летучих органических соединений, термостойкость, превосходную гибкость и ударопрочность, а также более низкие требования к техническому обслуживанию.
Преимущества автоосаждения по сравнению с традиционными операциями по нанесению покрытий включают значительно меньшее количество рабочей силы и оборудования, а также меньшее время цикла, энергии, обращения, упаковки и транспортировки.Его можно использовать в комбинированной последовательности отверждения с некоторыми верхними покрытиями из-за низкого содержания летучих органических соединений, и он является самоограничивающимся, поэтому его нельзя наносить чрезмерно. Покрытие также обеспечивает равномерную толщину всех деталей, включая края и сложные формы, без подтеков, потеков или провисаний.
Покрытия Henkel одобрены такими компаниями, как BMW, Volkswagen и PSA.
Surface Technology
Surface Technology — ведущий поставщик автомобильных покрытий и услуг по нанесению покрытий, среди клиентов которого Jaguar Land Rover, BMW, Volkswagen и Toyota.
Его услуги по нанесению покрытий включают порошковое покрытие, смазку сухой пленкой, цинк-никель, герметизацию пористости, цинкование и химическое никелирование. Области применения включают блоки цилиндров и головки цилиндров, компоненты системы кондиционирования воздуха, гидроусилитель рулевого управления и тормозные трубопроводы, топливопровод и системы подачи топлива, а также тормозные суппорты. Помимо антикоррозионных свойств, их покрытия также обеспечивают износостойкость, защиту от истирания, истирания, электроизоляцию, где это необходимо, а также стойкость к тепловой и серной коррозии.
BASF
BASF — еще один ключевой поставщик, который предлагает широкий спектр покрытий, красок и технологических процессов специально для автомобильной промышленности. В его портфель электронных покрытий входят Cathoguard 800 и Cathoguard 900 — новейшие технологии, которые не содержат олова в соответствии с нормативными требованиями и содержат менее 1% растворителей.
Эти катодные электронные покрытия наносятся во время погружения в резервуар для электроосаждения и защищают края, поверхности и полости автомобиля от коррозии.Для получения катодного электронного покрытия используется электрический ток для постоянного нанесения краски на кузов или компонент. Покрываемая деталь фактически становится катодом с отрицательным зарядом. Частицы связующего покрытия действуют как катионы с положительным зарядом. В ванне катодного электронного покрытия частицы покрытия перемещаются к стальному телу или детали с помощью электрического тока и осаждаются. Этот процесс обеспечивает идеальное покрытие для защиты от коррозии, так как все полости и края могут быть покрыты равномерно.
Резюме
В такой крупномасштабной отрасли отзывы того или иного рода неизбежны. Однако стоимость отнюдь не незначительна, а коррозия — одна из основных причин, по которым инициируются отзывы. Введение легких металлов в производство также поставило ряд новых задач, поскольку такие металлы, как магний, полезны для снижения веса, но подвержены коррозии. Для защиты различных материалов и компонентов от коррозии требуются различные подходы, и этот сектор автомобильной промышленности будет продолжать развиваться.
Испытания на коррозию
Коррозионные испытания имеют фундаментальное значение для понимания того, как материалы работают в смоделированных условиях эксплуатации, и могут помочь гарантировать, что они достигнут расчетного срока службы.
Испытания на коррозию используются в различных отраслях промышленности для различных областей применения.Они варьируются от упреждающих мер, таких как участие в процессах проектирования переднего плана, до реагирования на изменения в среде обслуживания, требований по снижению затрат и эффективности или для квалификации и выбора материалов и химикатов для обслуживания.
Поиск поставщика испытаний на коррозию с необходимыми возможностями, оборудованием, опытом, прочной репутацией и акцентом на передовые практики в области здравоохранения и безопасности может оказаться сложной задачей.
Хорошо разработанная программа выбора материалов и испытаний на коррозию является ключом к определению пригодности материалов для предполагаемых условий эксплуатации.
Коррозия может привести к необратимым повреждениям материалов, оборудования, активов и трубопроводов. Эти потери не только дорого исправить в денежном выражении, но и последующий отказ оборудования может привести к простоям производства, рискам для здоровья и безопасности и ущербу репутации.
Решения для испытаний на коррозию
Обладая одним из крупнейших в мире предприятий по испытанию материалов и коррозии, наша репутация лидера в области консультирования по вопросам коррозии и материалов не имеет себе равных.
Наши услуги по испытаниям на коррозию могут применяться во всех отраслях промышленности и охватывают от краткосрочных плановых испытаний с быстрым выполнением работ до долгосрочных индивидуальных проектов.
У нас есть опыт и возможности для проектирования и изготовления испытательных стендов для моделирования сложных производственных условий и оценки качества материалов в них.
Наше оборудование включает коррозионностойкие сосуды высокого давления, динамические автоклавы и проточные контуры. Диапазон используемых нами методов анализа включает расширенный электрохимический мониторинг, трехмерную лазерную профилометрию и сканирующую электронную микроскопию.
С нашей многопрофильной командой мы можем разработать уникальные решения для решения проблем, связанных со сложными или экстремально агрессивными средами.
В дополнение к индивидуальным испытаниям на коррозию мы можем проводить испытания по широкому спектру отраслевых стандартов, включая TM0177, TM0198 и TM0284, на наших предприятиях, аккредитованных UKAS.
Мы предлагаем испытания для классификации коррозионной активности продуктов в соответствии с рекомендациями ООН — Транспортировка опасных грузов, метод коррозии металлов С1 ООН, РАЗДЕЛ 37 ПРОЦЕДУРЫ КЛАССИФИКАЦИИ МЕТОДЫ И КРИТЕРИИ ИСПЫТАНИЙ ВЕЩЕСТВ КЛАССА 8, правила CLP, заявки BPR (Реестр биоцидных продуктов) ).
Использование наших услуг по испытаниям на коррозию обеспечивает Вам полную гарантию качества, в которой команды мирового класса работают над защитой ваших сотрудников и процессов и развитием вашего бизнеса на конкурентном рынке.
Отправьте нам заявкуНужна помощь или есть вопрос? +44 (0) 116 296 1620
Проблемы коррозии в инсинераторах и котлах, работающих на биомассе.
Инсинераторы широко используются для сжигания городских отходов, биоотходов, древесины, соломы и биомедицинских отходов.Сжигание этих типов отходов приводит к образованию хлоридов натрия и калия, которые могут повредить металлическую часть инсинератора. В котлах, работающих на биотопливе, присутствует аналогичная высококоррозионная среда. Была сделана попытка рассмотреть проблемы коррозии и их решения в соответствии с доступной литературой.
1. Введение
Сжигание — это высокотемпературный процесс, который превращает органические и горючие отходы в неорганические, горючие вещества и приводит к резкому уменьшению объема и веса отходов [1–3].Установки для сжигания отходов широко используются для удаления промышленных, опасных, неопасных, коммерческих, муниципальных, некоторых сельскохозяйственных и больничных отходов [4]. Обычно инсинераторы работают при высокой температуре от 300 ° C до 1100 ° C в зависимости от объема и типа отходов, инсинератора и используемого топлива [5]. В недавней литературе высказывается мнение, что сжигание является устаревшей технологией для обработки отходов, поскольку она ненадежна и создает вторичный поток отходов, более опасный, чем исходный [6]. Создание мусоросжигательного завода для утилизации опасных отходов было принято Агентством по охране окружающей среды США в 1976 году как «Закон о сохранении и восстановлении ресурсов PL 94-580.«Системы пост-управления дымовыми газами широко используются в мусоросжигательных заводах, чтобы уменьшить любой вред, который может быть причинен потоком дымовых газов. Эти системы состоят из таких устройств, как электрофильтр, скруббер Вентури, скруббер с уплотненным слоем, пластинчатая колонна, сухой скруббер, полусухой скруббер, рукавные фильтры или рукавные камеры, мокрый электрофильтр и ионизирующий мокрый скруббер [7]. Следовательно, вторичный поток может быть очищен, чтобы сделать его безвредным с помощью вышеупомянутого оборудования.
Поскольку за последние несколько десятилетий во всем мире значительно увеличилось количество отходов; сжигание биомедицинских отходов, твердых бытовых отходов и биомассы в котельных с псевдоожиженным слоем является привлекательным решением как для производства энергии, так и для сохранения земель, которые в противном случае выбрасываются на свалки [8, 9].Вывоз отходов на свалки может привести к загрязнению грунтовых вод, если свалка неправильно спроектирована или эксплуатируется [1]. В местах с высокой плотностью населения использование полигонов для захоронения отходов стало менее целесообразным, и сжигание отходов становится более привлекательным вариантом [10]. Ежегодно производятся миллионы тонн твердых бытовых отходов (ТБО), которые были переработаны с использованием технологии сжигания, которая снижает массу отходов на 70% и объем до 90%, а также обеспечивает энергию для производства электроэнергии [11].Отходы биомедицинской деятельности отражают реальную проблему живой природы и человеческого мира [8]. Неправильная утилизация медицинских отходов, шприцев и игл, которые собираются и используются повторно, может привести к распространению таких заболеваний, как гепатит С и СПИД [12]. Следовательно, желательно, чтобы такие отходы удалялись должным образом. Сжигание — это термический процесс, при котором уничтожается большая часть отходов, включая микроорганизмы [13]. Исследования показывают, что большинство инсинераторов работают при неправильной температуре и не уничтожают полностью отходы из-за использования недостаточного количества топлива [14].Необходимо адекватно окислить основные органические опасные отходы до уничтожения 99,99%. Почти полное уничтожение опасных отходов может быть достигнуто только при температуре около 1000 ° C и выше, когда могут быть обеспечены интенсивные условия реакции с помощью повышенной турбулентности в зоне горения, чтобы максимизировать реакцию и минимизировать время пребывания. Должно быть обеспечено адекватное давление для создания необходимой очистки от галогенов и твердых частиц [14]. Использование очень высокой температуры в мусоросжигательной печи приведет к разрушению строительного материала, тем самым уменьшив срок службы компонентов, работающих при более высоких температурах.
2. Проблема высокотемпературной коррозии в мусоросжигательной установке
Коррозионное повреждение является серьезной проблемой для мусоросжигательных заводов, которые требовали постоянного ремонта, что увеличивало эксплуатационные расходы [15]. В мусоросжигательных заводах часто встречается коррозия на стороне пожара [16]. Во время сжигания отходов и некоторых видов биомассы выделяются высокие уровни HCl, NaCl и KCl. Как хлориды, так и сульфаты, содержащие расплавы, могут образовываться на трубках пароперегревателя во время сжигания отходов. Расплавленные хлориды встречаются чаще из-за их более низких температур плавления [17].Миллер и Краузе [18] обнаружили, что накопление таких элементов, как сера, хлор, цинк, алюминий, калий, а иногда и свинец и медь, происходит на границе раздела металл / окалина в виде отложений в городских мусоросжигательных заводах. Ма и Роттер [19] сообщили, что городские твердые отходы содержат большое количество хлора как одного из свободных элементов, вызывающих высокотемпературную коррозию после того, как мелкие частицы летучей золы конденсируются на поверхностях теплообменников. Yokoyama et al. [20] предположили, что газообразный HCl, соли и сульфаты в слое вызывают коррозию труб теплообменника в установке для сжигания отходов с псевдоожиженным слоем, в то время как истирание происходит из-за сильного движения песка в слое.Агарвал и Гроссманн [21] обнаружили, что высокотемпературное коррозионное воздействие в мусоросжигательных заводах вызывается такими компонентами, как кислород, углерод, водород, азот, галогениды (Cl, F и Br), сера, фосфорорганические соединения, а также расплавленные соли и / или жидкость. разрушение металлов из-за присутствия металлов с низкой температурой плавления, таких как свинец, олово, сурьма, висмут, цинк, магний и алюминий. Отходы материалов в высокотемпературной области большинства установок для сжигания отходов в основном происходят из-за хлорирования и коррозии, вызванной хлоридом, хотя воздействие кислотно-щелочного флюсования, вызванное сульфатными отложениями, расплавленными хлоридами и эрозией, также может играть важную роль [21].
Сообщалось о нескольких исследованиях коррозии в среде мусоросжигательных заводов. Ishitsuko и Nose [22] обсуждают стабильность защитных оксидных пленок в среде сжигания отходов, таких как NaCl-KCl и NaCl-KCl-Na 2 SO 4 -K 2 SO 4 , проводимых на трех различных уровнях: основность. В среде сжигания отходов защитная пленка Cr 2 O 3 легко растворяется в расплавленных хлоридах, поскольку из-за расплавленных хлоридов имеет тенденцию иметь небольшую ценность из-за эффекта водяного пара, содержащегося в газообразных продуктах сгорания.Ли и др. [23] провели исследование различных сплавов на основе Fe с различным содержанием Cr и Ni, а также чистых металлов Fe, Cr и Ni. Исследования проводились в моделируемой среде мусоросжигателя при 450 ° C под отложениями ZnCl 2 -KCl в потоке чистого кислорода. Они пришли к выводу, что прилипание продуктов коррозии к подложке хуже для материалов с более высоким содержанием Cr, в то время как коррозионная стойкость к окружающей среде может быть значительно улучшена за счет увеличения содержания Ni, тогда как Zhang et al.[24] исследовали коррозионное поведение Fe и четырех промышленных сталей с различным содержанием Cr в окислительной атмосфере, содержащей HCl при температуре 500–600 ° C, что имитировало среду, в которой материалы обычно подвергаются воздействию в мусоросжигательной установке. Все образцы подверглись ускоренной коррозии. Они предположили, что увеличение содержания Cr в сплаве может улучшить их коррозионную стойкость. Сорелл [25] обнаружил, что в установках для сжигания твердых бытовых отходов преобладающими коррозионными веществами являются хлориды, обычно в сочетании с щелочными металлами [Na, K] и тяжелыми металлами [Pb, Zn].Новый дизайн зонда, состоящий из водоохлаждаемой фурмы поддержки, изготовленная из суперсплава на основе никеля с воздушным охлаждением, наконечник зондом, в котором образцы хранились между керамическими пластинами и зондом был введен в растение WTE [15]. На основании этого исследования они пришли к выводу, что коррозия в основном происходит из-за воздействия хлора при высоких температурах либо через газообразные частицы, такие как HCl или Cl 2 , либо частицы хлорида, которые осаждаются на трубах пароперегревателя, что приводит к сильному повреждению из-за ускорения образования оксидов [15] .Было также исследовано влияние добавления молибдена и кремния в стали, и было обнаружено, что в условиях горячей коррозии молибден, а также примерно до 1% кремния снижают скорость коррозии. Испытания проводились на ферритной стали T91 и аустенитной стали AC66 в нескольких атмосферах, присутствующих на угольных установках и мусоросжигательных установках, в нескольких смесях золы и при разной температуре. Время воздействия обычно составляло 100 часов, а иногда и 500 часов. На угольных электростанциях фактическое разложение зависит от содержания сульфатов щелочных металлов и SO 2 , а также от температуры.Присутствие HCl оказало небольшое влияние. В то время как в установке для сжигания отходов разложение было более выраженным, происходило развитие толстого, плохо прилипающего слоя коррозии с глубокой внутренней деградацией сплавов, которую приписывали активному окислению расплавленными хлоридами щелочных металлов [26]. Jegede et al. [27] также протестировали сплав Udimet и 310SS в дымовых газах, имитирующих сжигание отходов, при 750 ° C, изотермически в течение 72 и 120 часов, а также циклически в течение 120 часов. В обоих условиях субстрат демонстрировал первоначальное увеличение веса с последующей потерей веса после нескольких циклов.Они сообщили, что хлор образует летучие частицы, которые могут выделяться через потрескавшуюся окалину, оставляя после себя дефектную и пористую окалину. Ох и др. [28] обсуждали коррозионное поведение ряда коммерческих суперсплавов в потоке аргона-20%, кислорода и 2% хлора при 900 ° C. Они сообщили, что уменьшение массы сплавов может быть связано с образованием летучих хлоридов или оксихлоридов в качестве продуктов коррозии. Delay et al. [29] также подтвердили, что мобилизация щелочей и микроэлементов, присутствующих в клинических отходах, может привести к ускоренному разложению компонентов растения и может нанести ущерб окружающей среде.Ковино и др. [30] далее предположили, что установки для сжигания отходов имеют более серьезный температурный градиент, влияющий на проблемы коррозии, чем большинство камер сгорания угля, поскольку зола, откладываемая на заводах по переработке отходов в энергию (WTE), обычно содержит легкоплавкие плавленые соли и эвтектическую смесь, которая может привести к ускоренной коррозии. [30]. Ni et al. [31] определили состав летучей золы и состав зольной пыли установки для сжигания медицинских отходов (MWI), работающей в Китае. Они обсудили, что летучая зола в основном состоит из Ca, Al, Si, Mg, Na, O, C, Cl и S, а зольный остаток состоит из CaCO 3 , SiO 2 и Ca [OH] 2 . .Они также сообщили, что содержание хлора в летучей золе от MWI было выше, чем в летучей золе, производимой на установке для сжигания твердых бытовых отходов (MSWI).
3. Котел на биотопливе
Рост цен на топливо и усилия по обеспечению устойчивого производства энергии привели к освоению новых видов биотоплива как в энергетическом секторе для производства тепла и электроэнергии в котлах, так и в транспортном секторе для производства нового высококачественного транспортного топлива для использования непосредственно в двигателях [32].Было высказано мнение, что биомасса может быть единственным возобновляемым источником энергии, который может напрямую заменить традиционные ископаемые виды топлива [33]. Интеграция биомассы с парогазовыми газотурбинными электростанциями (ПГУ) дает повышение эффективности и возможное снижение затрат по сравнению с автономными установками [34]. В настоящее время около 12% мировой потребности в энергии генерируется за счет сжигания топлива из биомассы, которое варьируется от древесины и древесных отходов (например, от строительства или сноса) до сельскохозяйственных культур и черного щелока [35].Биомасса — это вид топлива, имеющий низкую плотность, объемный и выделяющий летучие вещества [36]. Топливо из биомассы сжигается в трех основных типах котлов, а именно в котлах с колосниковой решеткой, с барботажным слоем и в установках с циркулирующим псевдоожиженным слоем. Эти котлы обычно используются исключительно для выработки электроэнергии, но также могут использоваться для одновременного производства тепла и электроэнергии [37]. Обнаружено, что интерес к использованию биотоплива в энергетических целях растет по разным причинам, таким как снижение зависимости от импортируемой нефти, увеличение занятости в 20 раз, сокращение выбросов парниковых газов [38-40] и сокращение выбросов парниковых газов. кислотный дождь [41].Существует практическое правило, что совместное сжигание смесей топлива на основе отходов биомассы и угля с энергозатратой биомассы до 10% вызывает небольшое снижение выбросов N 2 O и может вызывать только легкие или практически не вызывать эксплуатационные проблемы [ 42]. Помимо этих преимуществ, некоторые технические проблемы, связанные с совместным сжиганием, включают проблемы подачи топлива, обращения и хранения, потенциальное увеличение коррозии, снижение общей эффективности, проблемы отложения золы, выбросы загрязняющих веществ, влияние выгорания углерода на маркетинг золы, влияние на выборочное каталитическое восстановление (SCR ) производительность и общая экономика [43].Проблема с подачей топлива возникает из-за того, что биотопливо имеет высокое содержание влаги, что увеличивает вес и тем самым увеличивает стоимость транспортировки. Это может увеличить стоимость, поскольку биомасса имеет низкую плотность энергии по сравнению с ископаемым топливом. Значительно больший объем топлива из биомассы требуется для выработки той же энергии, что и меньший объем ископаемого топлива, и поэтому это увеличивает стоимость. Низкая плотность энергии означает, что стоимость сбора и транспортировки топлива может быстро перевесить стоимость топлива; следовательно, его следует транспортировать с меньших расстояний [44].Также сообщалось, что многие электростанции, сжигающие топливо, такое как топливо из отходов, испытывают отказы пароперегревателей и / или повышенную коррозию водяной стенки из-за агрессивных компонентов топлива даже при низких температурах [45]. Одной из самых больших проблем, возникающих при сжигании биомассы, является повышенная тенденция к агломерации слоя и повышенное загрязнение поверхностей конвективного теплопередачи, иногда связанное с усилением коррозии. Наиболее разрушительное свойство биомассы по отношению к агломерации, обрастанию и коррозии, по-видимому, связано с ее зольными составляющими, такими как сера, хлор и фосфор [46].Хлориды щелочных металлов образуются при сгорании биомассы и переносятся в виде аэрозолей или в паровой фазе в газе сгорания, а затем осаждаются на металлической поверхности или на уже сформированном оксидном слое [47].
4. Коррозия и воздействие на окружающую среду в котле на биотопливе
В последние годы [48] в Швеции произошел переход от сжигания ископаемого топлива к биомассе с целью сокращения выбросов CO 2 . Сжигание 100% биомассы вызывает серьезные проблемы коррозии.Содержание хлора в древесине, торфе и угле относительно одинаково, но в древесном топливе значительно больше натрия и калия и меньше серы, и предполагается, что образование сложных хлоридов щелочных металлов в основном вызывает проблемы коррозии. Опыт шведских электростанций, работающих на 100% древесном биотопливе, показал, что традиционные стали для пароперегревателей (низкохромистые ферритные стали) необходимо заменять примерно через 20 000 часов, если температура пара составляет 470 ° C или выше [48].Хендерсон и др. [49] сообщили, что большинство видов топлива из биомассы имеет высокое содержание щелочных металлов и хлора, но они содержат очень мало серы по сравнению с ископаемым топливом. Наиболее опасным щелочным металлом для древесины является калий. Большая часть калия выделяется в газовую фазу во время горения и в основном присутствует в виде хлорида калия [KCl] и гидроксида калия [KOH]. Щелочные металлы образуют соединения с низкими температурами плавления и могут конденсироваться в виде хлоридов, вызывая массовое загрязнение труб перегревателя и другие эксплуатационные проблемы во время горения.На рис. 1 показана корродированная труба пароперегревателя на установке мощностью 100 МВт, работающей на биомассе с высоким содержанием хлора (> 1%) и битуминозном угле [50].
Хлор может вызвать ускоренную коррозию, приводящую к усиленному окислению, потере металла, внутреннему разрушению, образованию пустот и рыхлым отложениям. Ожидается, что наиболее серьезные проблемы коррозии в системах, работающих на биомассе, будут возникать из-за богатых хл отложений, образующихся на трубах пароперегревателя [51]. Viklund et al. [52] провели испытания на коррозию в котле-отходах при кратковременном воздействии (3 часа) для анализа состава отложений и начальной коррозии, а также при длительном воздействии (1550 часов) для исследования скорости коррозии.Эти исследования проводились с ферритными сталями 13CrMo44 и HCM12A, аустенитными сталями Super 304, 317L, Sanicro 28 и сплавами на основе никеля Hastelloy C-2000 и Inconel 625. Анализ показал, что в осадках преобладают CaSO 4 , KCl и NaCl, но также значительные количества смесей легкоплавких солей, таких как ZnCl 2 -KCl, PbCl 2 -KCl, FeCl 2 -KCl и NaCl-NiCl 2 . Измерения потерь металла показали неприемлемо высокие скорости коррозии для 13CrMo44, HCM12A и Super 304.Коррозионное воздействие на эти сплавы проявлялось в образовании смешанных отложений хлорида металла / оксида металла. Другой тип поведения наблюдался для высоколегированных аустенитных сталей и сплавов на основе никеля, которые были способны образовывать богатый хромом оксид рядом с металлом. Однако эти сплавы пострадали от некоторого локального питтинга. Такое поведение объясняется растворением оксида в расплавленных солях, присутствующих в осадке [52]. Reidl et al. [53] обнаружили, что основными видами топлива из биомассы, используемыми в Австрии, являются древесная щепа и опилки.Они сообщили о серьезной коррозии на нескольких установках для сжигания древесной щепы и коры, оборудованных водогрейными котлами с дымовыми трубами, что привело к утечкам из трубок теплообменников менее чем через 10 000 часов работы. Uusitalo et al. [54] сообщили, что сильная коррозия произошла в окислительных условиях имитируемой среды котла, работающего на биотопливе, где образцы подвергались воздействию синтетической соли, содержащей 40 мас.% K 2 SO 4 , 40 мас.% Na 2 SO 4 , 10 мас.% KCl и 10 мас.% NaCl при 550 ° C в окислительной и восстановительной атмосфере в течение 100 ч.Коррозионные испытания проводились на низколегированной ферритной стали и аустенитной нержавеющей стали, покрытии HVOF (Ni-50Cr, Ni-57Cr, Ni-21Cr-9Mo и Fe 3 Al), лазерной наплавке (Ni-53Cr) и диффузионном хромировании. стали. Они также сообщили, что оксиды на границах выступов подверглись воздействию хлора, через который он проникал [54]. Карлссон и др. [55] сообщили о влиянии NaCl, KCl и CaCl 2 на коррозию в бойлере, работающем на биомассе, и предположили, что CaCl 2 менее агрессивен по сравнению с NaCl и KCl.Они также предположили, что присутствие KCl и NaCl сильно ускоряет высокотемпературную коррозию нержавеющей стали 304L в среде 5% O 2 + 40% H 2 O с азотом в качестве газа-носителя при 600 ° C. Коррозия инициируется образованием хромата щелочного металла [VI] в результате реакции щелочи с защитным оксидом. Хроматообразование является стоком хрома в оксиде и приводит к потере его защитных свойств. Петтерссон и др. [56] изучали влияние KCl на аустенитную нержавеющую сталь 304 в присутствии 5% O 2 и 5% O 2 + 40% H 2 O окружающей среды при 400–600 ° C для времени выдержки 1 неделя.Их исследования показали, что KCl является сильно коррозионным веществом, и максимальная коррозия наблюдается при 600 ° C. Коррозия инициируется реакцией KCl с оксидом хрома, который обычно образует защитный слой на сплаве. В результате этой реакции образуются частицы хромата калия, оставляя на поверхности сплава оксиды с низким содержанием хрома. Петтерссон и др. [57] также сообщили о влиянии KCl, K 2 SO 4 и K 2 CO 3 и пришли к выводу, что KCl и K 2 CO 3 сильно ускоряют коррозию 304L, в то время как K 2 SO 4 мало влияет на скорость коррозии.Sharp et al. [58] предположили, что щелочные металлы и хлор, выделяемые в биотопливных котлах, вызывают ускоренную коррозию и засорение при высокой температуре пара пароперегревателя, из-за чего они должны работать при более низкой температуре, чем у современных котлов, работающих на ископаемом топливе, что приводит к снижению эффективности. . Hernas et al. [59] подтверждают, что высокотемпературная коррозия роторных подогревателей воздуха во время сжигания биомассы и угля происходит из-за присутствия хлоридов щелочных металлов в отложениях.Карлссон и др. [60] изучили коррозию котлов, работающих на биотопливе, и пришли к выводу, что коррозия в основном вызывается хлоридами щелочных металлов и хлористым водородом. Исследования [61] были проведены на двух жаропрочных сталях, Sandvik 8LR30 [18Cr 10Ni Ti] и Sanicro 28 [27Cr 31Ni 4Mo], чтобы определить роль отложений золы в мусоросжигательной установке и электростанции, работающей на соломе / древесине. Зола для этого исследования собиралась из секций радиационной камеры, пароперегревателя и экономайзера как на электростанциях, работающих на сжигании отходов, так и на электростанциях, работающих на соломе / древесной щепе.Они проводили эти исследования в лаборатории при температуре дымовых газов 600 ° C и температуре металла 800 ° C в течение 300 часов, подвергшихся воздействию HCl и SO 2 . Они сообщили, что и агрессивные газы, и зольные отложения синергетически увеличивают скорость коррозии из-за реакции между хлоридом калия с диоксидом серы и кислородом, которая приводит к образованию пористого незащищенного оксида [61]. Присутствие таких элементов, как хлор и цинк, вместе с щелочными металлами из биомассы может образовывать липкие соединения, которые увеличивают скорость роста отложений и быстро увеличивают скорость коррозии [62].Успешная работа установок сжигания зависит от способности контролировать и смягчать проблемы, связанные с золой, что может снизить эффективность, производительность и доступность оборудования, тем самым увеличивая стоимость электроэнергии. К таким проблемам относятся засорение, закупорка, коррозия оборудования и выбросы загрязняющих веществ [63]. Выдувание сажи — наиболее распространенный метод уменьшения воздействия отложений на теплопередающие трубки [62]. Один из способов уменьшить коррозию при пожаре — это изменить окружающую среду с помощью топливных добавок, таких как сера.Было также обнаружено, что сульфат аммония снижает скорость роста отложений и вдвое снижает скорость коррозии ферритных / мартенситных сталей в дровяном котле. При добавлении сульфата в оксиде образовывались сульфиды железа, которые, как полагают, препятствовали процессу коррозии, а хлориды железа в основном отсутствовали [64]. Viklund et al. [64] также обнаружили, что добавление сульфата аммония в котлы, работающие на биомассе, снижает склонность к коррозии. Облучение на месте проводилось в котле с ЦКС мощностью 75 МВт в Хендельё, Швеция.Завод сжигает 30–50% бытовых отходов и 50–70% промышленных отходов, и было обнаружено, что в отложениях преобладают Na, K, Ca, Cl, S и O. Низколегированная ферритная сталь EN1.7380 [Fe- 2.25Cr-1Mo] и аустенитный EN1.7380 [Fe-18Cr-9Ni] экспонировались в течение 4 часов на зондах с воздушным охлаждением. Металлография показывает заметную разницу в коррозионном воздействии между двумя сталями. Было высказано предположение, что добавление 300 ppm SO 2 приводит к резкому снижению скорости коррозии, так как это приводит к образованию K 2 SO 4 , который не реагирует с Cr 2 O 3 , а также подавляет образование отложений, богатых хлоридами щелочных металлов.Добавление серы или серосодержащих соединений в топливо привело к снижению скорости коррозии подвергнутого воздействию образца на 50–70%. Карлссон и др. [65] сообщили, что добавление осадка пищеварительных сточных вод в котел CFB мощностью 12 МВт в Технологическом университете Чалмерса привело к снижению скорости коррозии 304L и Sanicro 28 при 600 ° C после 24 часов воздействия. Ли и др. [66] сообщили, что добавление извести или MgO с дутьем снижает коррозию, поскольку магний соединяется с ванадием с образованием ванадата магния, который является твердым при температуре котла.Добавление каолина (Al 2 O 3 · SiO 2 ) может значительно уменьшить отложения в перегревателе, коррозию и шлакообразование и, таким образом, улучшить работу котла, работающего на биомассе [67]. Каолин, которого много в каолините (Al 2 Si 2 O 5 (OH) 4 ), используется для улавливания паров щелочных металлов, выходящих из области горения [68, 69].
5. Меры по исправлению положения
Guilemany et al. сообщили о возможном решении для окисления стальных труб теплообменников с помощью покрытий HVOF термическим напылением и пришли к выводу, что проволочные и порошковые покрытия HVOF показывают хорошие свойства для защиты стальных труб теплообменников от эрозии, вызванной воздействием золы в дымовых газах [103].Резахами [119] сравнил эффект моделируемой среды котла, работающего на жидком топливе (70% V 2 O 5 -20% Na 2 SO 4 -10% NaCl при температуре 550 ° C и 650 ° C для 6 циклов по 48 часов каждый) на различных ферритных и аустенитных сталях, а также на некоторых покрытиях, нанесенных термическим напылением. Аустенитная сталь подвержена равномерной коррозии, тогда как ферритная сталь подвержена коррозии по границам зерен. Термически напыленные покрытия FeCrAl, 50Ni-50Cr, Tafaloy 45LT и Cr 3 C 2 NiCr также были испытаны в заданных условиях, и результат показал, что все покрытия обеспечивают хорошую устойчивость к коррозии и помогают увеличить срок службы обоих. стали [119].Singh et al. [120] исследовали поверхностно применяемый Y 2 O 3 в качестве ингибитора, который приводит к снижению высокотемпературной коррозии жаропрочных сплавов в присутствии Na 2 SO 4 -60V 2 O 5 при 900 ° C. в циклическом режиме. Goyal et al. [121] подтверждают, что добавление ингибитора, такого как ZrO 2 , в среду котла, например Na 2 SO 4 -60% V 2 O 5 , может помочь в снижении скорости коррозии суперсплавов при высоких температурах. температура.Ямада и др. [106] протестировали D-пушку, HVOF и покрытие из сплава 50% Ni-50% Cr с плазменным напылением на стали и суперсплавах на основе Ni в реальных условиях сжигания мусора. Анализ выявил присутствие хлора, который является основной причиной горячей коррозии на покрытых поверхностях. Покрытия, нанесенные распылением с помощью пистолета D-распылителя, обеспечивают максимальную коррозионную стойкость в котле фактического мусоросжигательного завода, работающего без каких-либо проблем в течение 7 лет и, как ожидается, будут иметь более длительный срок службы. Пол и Харви [122] протестировали коррозионную стойкость покрытия из четырех сплавов Ni, нанесенного методом HVOF на подложку P91, в условиях моделирования высокотемпературного горения биомассы.Было замечено, что покрытие из сплава 625, NiCrBSiFe и сплава 718 работает лучше, чем сплав C-276.
6. Обсуждение
Спрос на производство электроэнергии постоянно растет с увеличением населения. В Индии спрос на электроэнергию ежегодно увеличивается до 3,6%. Большая часть этой энергии производится из ископаемого топлива, такого как уголь и т. Д. Сжигание угля приводит к выбросу парниковых газов, таких как двуокись углерода, что вызывает глобальное потепление. Эти газы вызывают загрязнение окружающей среды.Добыча угля также ведет к ухудшению состояния окружающей среды. Следовательно, использование биотоплива или органических и других отходов для выработки электроэнергии может дать два основных преимущества. Требуются два требования: во-первых, сократить использование ископаемого топлива и, во-вторых, сохранить площадь отходов на свалках. Технология сжигания в настоящее время используется для удаления твердых бытовых отходов, биоотходов и медицинских отходов. В случае медицинских отходов необходима более высокая температура сжигания для уничтожения микроорганизмов во избежание распространения болезней.Тип окружающей среды в установке для сжигания отходов будет зависеть от типа сжигаемых топливных отходов.
При сжигании городских отходов образуются такие соединения, как ZnCl 2 , PbCl 2 , KCl и NaCl, тогда как при сжигании соломенных отходов образуются более высокие концентрации KCl и K 2 SO 4 . При сжигании древесины будет образовываться большее количество NaCl и Na 2 SO 4 вместе с KCl и K 2 SO 4 , тогда как уголь в качестве топлива приведет к образованию солей, таких как Na 2 SO 4 , K 2 SO 4 и (NaK) 2 (FeSO 4 ) 3 .Производство всех таких видов материалов приводит к коррозии, которая нарушает основные свойства металлов из-за воздействия коррозионных соединений на поверхность металла. Информация о поведении различных сплавов и покрытий сведена в Таблицу 1.
|
CRC Long Life Anti Rust — Антикоррозийный спрей для предотвращения ржавчины
Когда дело доходит до продуктов для защиты от ржавчины, CRC Long Life Anti Rust — это полный пакет.Обеспечивает превосходную смазку и долгосрочную защиту от ржавчины для всех металлов, подверженных ржавчине и солевой коррозии. Это отличный ингибитор ржавчины и смазка для продления срока службы металлических поверхностей скольжения и вращения. CRC Long Life Anti Rust проникает и покрывает металлические поверхности, вытесняя влагу и обеспечивая защиту от ржавчины, предотвращая попадание влаги в будущем.
CRC Long Life — это прозрачная, свободно протекающая жидкость, которая безопасна для использования в большинстве ситуаций, легко наносится и удаляется при необходимости.
CRC Long Life рекомендуется в качестве финальной пленки, используемой для прецизионных поверхностей машин, и в качестве защитного, противозадирного покрытия для сборок, находящихся на хранении или при транспортировке. CRC Long Life также используется в качестве стартовой смазки для хранимого оборудования.
CRC Long Life Anti Rust защищает стальные детали внутри помещений на срок до 2 лет. Он не содержит CFC, хлорированных растворителей или силикона.
Диапазон температур от -20 ° C до + 150 ° C. Утверждено MPI C12.
Особенности и преимущества
- Защита инструментов, машин и общего оборудования при длительных простоях
- Защищает блоки цилиндров, поршни и детали от атмосферной коррозии
- Идеально для сезонных «консервации» судовых двигателей и хранения без коррозии
- Не содержит CFC, хлорированных растворителей и силикона
- Безопасно использовать в большинстве ситуаций
- Безопасен для использования на большинстве поверхностей, включая резину, ткань, пластмассы и краски.
- Легко наносимый аэрозоль — для контролируемого нанесения антикоррозийным распылением
- Поставляется оптом 4 л.
- Выдерживает 350 часов испытания в солевом тумане
- Защищает стальные детали внутри помещений до 2 лет
- Не требует очистки перед использованием оборудования
- Диапазон температур от -20 ° C до + 150 ° C
- Проникает для вытеснения влаги — предотвращает попадание влаги в будущем
- Непроводящие ингибиторы коррозии
- Легко удаляется обезжиривающими средствами CRC Lectra Clean или CRC Brakleen, если требуется.